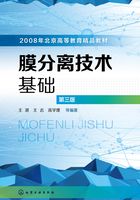
2.5 膜的制备
膜分离技术的核心是分离膜。衡量一种分离膜有无实用价值,要看是否具备以下条件:高选择性;优异的抗物理、化学和微生物侵蚀的性能;足够的柔韧性和机械强度;使用寿命长,适用 pH范围广和成本合理,制备方便,便于工业化生产。
2.5.1 高分子膜的制备
许多有机高分子都可以做成薄膜,但若要成为具有高性能且有实用价值的分离膜,除了选择合适的膜材料外,同样重要的是必须找到一种使其具有合适结构的制造工艺技术。有机高分子分离膜从形态结构上可分为对称膜(或称均质膜)和非对称膜两大类[4]。
2.5.1.1 均质膜
(1)致密均质膜 致密均质膜由于太厚,渗透通量太小,一般较少实际应用于工业生产。有机高分子的致密均质膜在实验室研究工作中广泛用于表征膜材料的性质。其制备方法如下:
①溶液浇铸。将膜材料用适当的溶剂溶解,制成均匀的铸膜液, 将铸膜液倾倒在玻璃板上(一般为经过严格选择的平整玻璃板),用特制的刮刀使之铺展开,成为具有一定厚度的均匀薄层,然后移置到特定环境中让溶剂完全挥发,最后形成均匀薄膜。
②熔融挤压。一些有机高分子找不到合适的溶剂制成铸膜液,则要采用熔融挤压法来成膜,将高分子材料放在两片加热了的夹板之间,并施以高压(10~40MPa),保持0.5~5min后,即可得到所需的膜。
③不同聚合物之间形成的致密膜。在聚合反应过程中,由于反应热的产生会出现聚合自动加速现象,由此引发交联并生成高分子量聚合物,它是由于各种链转移和偶联反应的交联作用。这类致密均质膜必须在聚合期间就形成。属于这一范畴最主要的膜类型是均质离子交换膜。
(2)微孔均质膜
①径迹刻蚀法。径迹刻蚀法主要分两个步骤:首先用荷电粒子照射高分子膜,使高分子膜化学键断裂,留下敏感径迹,再将膜浸入适当的化学刻蚀试剂中,高分子的敏感径迹被溶解而形成垂直于膜表面、规整的圆柱形孔。目前,用于制备核径迹膜的材料主要是聚酯和聚碳酸酯,制得膜的孔径范围为0.01~12μm,孔密度可达2×108个/cm2 (图2-6)。

图2-6 聚碳酸酯NTM断面SEM照片[12]
②拉伸法。一般要经过两步。首先将温度已达其熔点附近的高分子经过挤压,并在迅速冷却的条件下制成高度定向的结晶膜,然后将该膜沿机械力方向再拉伸几倍,这次拉伸破坏了它的结晶结构,并产生裂缝状的孔隙,这种方法一般称为Celgrad法。Celgrad法选用商品聚丙烯为膜材料,在拉出速率远高于挤出速率的情况下,聚丙烯分子本身变为一种与机械力成一致方向的微纤维形式,它会在机械力垂直方向上形成的折叠链排薄片的微晶中起核心作用。然后,在低于高分子的熔融温度、高于起始的退火温度下进行拉伸,使薄片之间的非晶区变形为微丝,结果形成了一种顺着机械力方向的具有狭缝隙的多孔互联网络,孔的尺寸取决于拉伸后的微丝。表2-2说明Celgrad薄膜具有优良的机械物理性质。Core-Tex是另一种采用拉伸成孔的微孔分离膜。
表2-2 Celgrad薄膜的典型机械物理性质

①MD=机械力方向。
②TD=横切于机械力方向。
③溶出法。在难溶的高分子材料中掺入某些可溶性的组分,制成均质膜后,再用溶剂将可溶性组分浸提出来,形成微孔膜。这种方法仅用于制备难溶性聚合物分离膜。
④烧结法。使一个微小颗粒或者一群均匀组成的微粒在高温条件下聚集,没有任何形状的改变。烧结不是一个简单的致密化作用,对高分子物质进行烧结作用,微粒表面必须足够软化,以使大分子链段相互扩散而进入邻近的微粒中去。制备高分子膜的烧结过程,主要限于具有柔性结构的高分子。用烧结法制备的膜一般孔径分布均较宽,但是它们具有相当高的强度和抗压实性,以及这些高分子的化学惰性等,使它们在某些特殊分离中仍得到应用。
(3)离子交换膜 用于电渗析膜过程的有机高分子荷电均质膜。根据膜中活性基团分布的均一程度,离子交换膜大体上可分为异相膜、均相膜和半均相膜三类。若根据在膜本体上的不同电性能,离子交换膜可分为阳离子交换膜和阴离子交换膜两大类。阳离子交换膜的活性基团则为胺、叔胺和仲胺等。最常用的离子交换膜材料有:聚乙烯、聚丙烯和聚氯乙烯等的苯乙烯接枝高分子。
①异相离子交换膜。形成膜的整个材料不是呈一相存在的膜叫异相膜,例如离子交换树脂粉加上黏合剂和增塑剂后热压所成的膜即为异相膜。热压成型法是制备异相离子交换膜最常用的方法。
②均相离子交换膜。制备方法有五种:a.将能反应的混合物(即酚、苯磺酸、甲醛)进行缩聚。混合物中至少有一种能在它的某一部分形成阴离子或阳离子。b.将能反应的混合物(即苯乙烯、乙烯基吡啶和二乙基苯)进行聚合。混合物中至少有一种含有阴离子或阳离子,或者有可以成为阴离子或阳离子的部位。c.将阴离子或阳离子基团引入高分子或高分子膜。例如将苯乙烯浸入聚乙烯薄膜内,使浸入膜内的单体聚合,形成聚苯乙烯,然后将聚苯乙烯进行磺化。与此类似,也可通过接枝聚合将离子基团接到高分子薄膜的分子链上。d.将含有阴离子或阳离子的一部分引到一个高分子上(例如聚砜),然后将此高分子溶解并浇铸成膜。e.通过把离子交换树脂高度分散于一高分子中形成高分子合金或共聚体。无论用以上哪一种方法制备,所制膜都需用织物增强,以改善其强度及形态稳定性。均相离子交换膜的性能远优于异相膜,所以目前使用的离子交换膜多为均相膜。
③半均相离子交换膜。从宏观上看,是一种均匀一致的整体结构,成膜的高分子化合物与具有离子交换特性的高分子化合物十分紧密地结合为一体,但都不是化学键结合。从微观上看,应属于异相膜范畴,习惯上也可将此膜看作是均相离子交换膜。其制备方法和异相和均相离子交换膜类同。
2.5.1.2 非对称膜
非对称膜一般比均质膜的渗透通量要高得多,由薄的致密皮层(起分离作用)和多孔支撑层(起支撑皮层作用)构成,包括相转化膜和复合膜。
(1)相转化膜 将均相的高分子铸膜液通过各种途径使高分子从均相溶液中沉析出来,使之分为两相:一相为高分子富相,最后形成高分子膜;另一相为高分子贫相,最后成为膜中之孔。相转化法制备的高分子非对称膜具有以下特点:皮层与支撑层为同一种材料;皮层与支撑层是同时制备形成的。相转化法制膜的方法包括有:
①溶剂蒸发法(干法)[13,14]。高分子材料溶于一双组分溶剂混合物,此混合物由易挥发的良溶剂(如氯甲烷)和相对不易挥发的非溶剂(如水和乙醇)组成。将此铸膜液在玻璃板上均匀涂覆成具有一定厚度的薄层,随着易挥发良溶剂的不断蒸发逸出,非溶剂的比例愈来愈大,高分子沉淀析出,形成薄膜,这一方法也称为干法。这是相转化制膜工艺中最早的方法,1920~1930年就被Bechhold等使用[图2-7(a)]。
②水蒸气吸入法[15]。高分子铸膜液在一平板上铺展成一薄层后,在溶剂蒸发的同时,吸入潮湿环境中的水蒸气使高分子从铸膜液中析出进行相分离,这一过程的相图见图2-7(b)。此法是商品相转化分离膜的常用生产方法。典型的铸膜液组成为:膜材料(醋酸纤维素与硝酸纤维素)、溶剂(丙酮、水、乙醇、乙二醇)。

图2-7 溶剂蒸发法制备多孔膜的铸膜液组成变化相图(a)和水蒸气吸入法制备多孔膜的铸膜液组成变化相图(b)
③热致相分离法[16]。又称TIPS法,是Castro发明的。它使用稀释剂(高温时对高分子膜材料是溶剂,低温时是非溶剂),将聚合物与稀释剂在高温下溶解成均匀铸膜液,将铸膜液涂覆成一定形状的膜,然后降低温度冷却使其固化。具体步骤如下:a.在高温下将高分子膜材料与低分子稀释剂熔融混合成一均匀的溶液;b.将溶液制成所需的形状(平板或中空);c.将溶液冷却使之发生相分离;d.将稀释剂从膜中去除(溶剂抽提)。TIPS法主要适用于结晶和半结晶性高聚合物,如聚烯烃、聚丙烯、聚偏氟乙烯等。TIPS法制膜过程的温度-组成相图见图2-8,图中,ϕm为偏晶点,Tc为结晶点。该方法可用于制备平板膜和中空纤维膜。
④非溶剂致相分离法(NIPS法)。由Loeb和Sourirajan在1960年发明。在相同截留率情况下,NIPS法制备的非对称醋酸纤维素反渗透膜的通量为均质膜的10倍左右,这成了分离膜发展的里程碑。电子显微镜观察发现,这种膜具有薄、非常致密的皮层以及海绵状疏松的多孔支撑层。后人将这种方法称为L-S相转化法,并将它推广用于其他高分子非对称膜的制备。图2-9是L-S法制备非对称膜的流程。

图2-8 液-液与固-液相分离的温度-组成相图[17]

图2-9 L-S法制膜流程示意图
1—料液槽;2—刮刀;3—水位调节器;4—凝胶槽;5—牵引滚;6—织物卷;7—涂覆卷;8—擦胶刀;9—缠绕液;10—洗涤槽;11—流量计
三元体系完整的相图如图2-10所示,细分为四个区域:Ⅰ是单相溶液区,由聚合物-溶剂轴和浊点线或称双节线构成。Ⅱ是液-液两相区;在两相区,旋节线又划出亚稳区和非稳区,浊点线与旋节线之间是亚稳区,旋节线右边是非稳区。Ⅲ是固-液二相区。Ⅳ是单相玻璃态区。连接线表示聚合物富相与贫相相对应的平衡浓度,玻璃化转变线以上区域是固态单相区,铸膜液进入该区则形成固态。

图2-10 三元体系典型相图[18,19]
1—溶液单相区;2—双结线(浊点线);3—玻璃化转变线;4—玻璃单相区;5—液-液两相区;6—旋节线;7—连接线;Ⅰ—均相区;Ⅱ—亚稳区;Ⅲ—不稳区
NIPS法制备非对称分离膜步骤复杂,影响因素较多。为了使膜的性能获得良好的重现性,操作时应注意:高分子材料与溶剂的纯化;高分子材料-溶剂-添加剂的完全溶解与熟化;铸膜液中机械杂质的除去;流涎用玻璃板的洁净;铸膜液流涎时气体夹带的预防;维持制膜和溶剂蒸发时环境温度、湿度与气氛的恒定等。
(2)复合膜[20~23] 分离膜的透水速度与其致密皮层的厚度大致成反比,所以降低相转化法制备的高分子非对称分离层的厚度是提高膜渗透通量的有效途径。J.E.Anderson等根据高分子溶液的松弛理论,计算出CA/丙酮体系非对称反渗透膜的皮层厚度为100μm,再变薄就困难了。另外,高分子膜在压力下被压密可使膜的渗透通量下降。相转化法制备的非对称反渗透膜的压密主要发生在介于表面致密层和下部多孔支撑层之间的过渡层。假如采用其他制膜工艺,分别制备致密皮层和多孔支撑层,则既可减少致密皮层的厚度,又可消除易引起压密的过渡层,从而提高膜的渗透通量和抗压密性,这是当年制作复合膜工艺的基本思路。复合膜具有以下特点:①可分别优选不同的膜材料制备致密皮层(也称超薄脱盐层)和多孔支撑层,使它们的功能分别达到最佳化;②可用不同方法制备高交联度和带离子性基团的致密皮层,从而使膜对无机物,特别是对有机低分子具有良好的分离率,以及良好的物理化学稳定性和耐压密性;③大部分复合膜可制成干膜,有利于膜的运输和保存。
1963年Riley采用首先制备多孔支撑层,然后在多孔支撑层上制备超薄分离层,制备了反渗透复合膜。目前,绝大部分复合膜以聚砜多孔膜为支撑膜,致密层厚度一般可达50μm 左右,最薄的为30μm。在支撑膜上形成致密层的方法有:
①高分子溶液涂覆。将多孔支撑膜的上表面与高分子稀溶液相接触,然后阴干。Riley等首先采用这种方法制备了以醋酸纤维素为支撑膜的三醋酸纤维素(CTA)反渗透复合膜。
②界面缩聚。这是指两种可反应的单体分别溶于互不相溶的溶剂中,当两相接触时就在基膜表面直接进行界面反应,形成超薄脱盐层。1960年,Cadotte 首次采用这种方法制备了NS-100反渗透复合膜。界面缩聚法与就地聚合法是复合膜制备中最主要的两种方法,PA-300、FR-30等具有优良性能的一级海水淡化反渗透膜都是采用界面缩聚法制备的[24]。
③原位聚合(单体催化聚合)。它是将支撑膜浸入含有催化剂并在高温下能迅速聚合的单体稀溶液中,取出支撑膜并排去过量的单体稀溶液,然后在高温下进行催化聚合。美国Borth Star研究所采用该法成功研制了NS-200反渗透膜复合膜。
④等离子体聚合。将某些在辉光放电下能进行等离子体聚合反应的有机小分子直接沉积在多孔支撑膜上,反应后得到以等离子体聚合的高分子为超薄脱盐层的复合膜。等离子体聚合反应通常采用具有内部电极联系的钟罩式反应器和无电极的管式反应器。几乎所有的有机物都能进行等离子体聚合,但不一定都能形成具有选择透过性的薄膜。许多含氮、含烯烃双键的有机化合物(例如含有NH、—NH2,—CH
CH—等基团的有机物),特别是芳香胺类能形成具有优良反渗透特性的高分子沉积薄层;含氧、含氯的有机物(例如含有—CO—、—COO—、—O—、—OH等官能团)以及脂肪烃和环烷烃,由于在辉光放电时易分解,不宜作等离子聚合物的单体。日本住友化学公司研制的Slolcon膜是唯一的商品化等离子复合膜。
⑤动态自组装膜。经加压闭合循环流动的方式,使胶体粒子或微粒附着沉积在多孔支撑体表面以形成薄层底膜,然后再用高分子聚电解质稀溶液同样以加压闭合循环流动的方式,将它附着沉积在底膜上,构成具有溶质分离性能、有双层材料的反渗透复合膜,这种复合膜称为动态自组装膜(动态膜)。几乎所有的无机与有机聚电解质都可以作为动态自组装的制膜材料。在无机电解质中有Al3+、Fe3+、Si4+、Zr4+、Th4+、V4+、U4+等的水合氧化物或氢氧化物,其中Zr4+的性能最好;在有机聚电解质中有聚丙烯酸、聚乙烯磺酸、聚马来酸、聚乙烯胺、聚苯乙烯磺酸、聚乙烯基吡啶、聚谷氨酸等;某些中性的非聚电解质(如甲基纤维素、聚氧化乙烯、聚丙烯酰胺)以及某些天然物(如黏土、腐殖酸、乳清、纸浆废液等)也能作为动态膜材料。动态自组装膜的多孔支撑体可用陶瓷、烧结金属、烧结玻璃、碳等无机材料以及醋酸纤维素、聚氯乙烯、聚酰胺、聚四氟乙烯树脂等有机烧结材料。多孔支撑体孔径范围通常要求为 0.01~1μm,与材质有关。最适宜范围为0.025~0.5μm,厚度没有特别限制,根据使用要求,只需保证足够的机械强度。动态自组装膜也可制成单层结构的超滤膜。
⑥水面展开法。将高分子溶液铺展在水面上,铺展成超薄膜,将其覆盖在多孔支撑膜上就形成复合膜。它可以是间歇式操作,也可以是连续式操作,为了避免超薄层上的缺陷,还可采用反复多层制备超薄层的方法。
一般来说,反渗透膜复合膜在具有高脱盐率的同时,比相转化法非对称膜的渗透通量也高出许多。复合膜的出现使反渗透海水淡化成本大幅度下降,而且促进了其他膜分离过程的开发。
2.5.2 无机膜的制备方法
无机膜的制备技术[25,26]主要有:采用固态粒子烧结法制备载体及过渡膜,采用溶胶-凝胶法制备超滤、微滤膜,采用分相法制备玻璃膜,以及采用专门技术(如化学气相沉积、无电镀等)制备微孔膜或致密膜。
致密的金属膜主要指的是钯膜。以压延法制造的致密金属膜,厚度约为25μm。更薄的膜是在多孔体上以喷溅、电化学沉积、化学气相沉积等技术制造的。钯膜只在小型系统中应用。由于气体透过量和膜厚成反比,金属用量和膜厚成正比,超薄金属膜具有更好的性能。
陶瓷膜的制造方法主要有:①烧结法,即将胶体(或粉体)形成的薄层烧结而得,孔径较大,约10~100μm;②沥浸法,即将混相的玻璃箔或毛细管于酸中溶去一相;③溶胶-凝胶法,此法先制备溶胶,一种称Particulate法,以相应的醇盐水解、解胶及陈化而得;另一种称Polymeric法,在大量含醇盐的醇溶液中引进水,使醇盐在分子水平上水解并聚合。
相转移法制造的多孔玻璃孔径均匀、孔隙率大,是优良的过滤膜及基膜。
将聚合物的中空纤维在惰性气体中或真空中加热而分解成为碳分子筛膜,孔径约0.2~0.5nm。沥浸法亦可制得孔径小于1nm的分子筛膜玻璃纤维。
(1)金属致密膜的制备
①电镀法。控制直流电压和温度,将金属或金属合金沉积在阴极的支撑体上而形成薄膜。金属钯比较容易在平板和管式支撑体上镀膜。钯膜的厚度主要通过电镀时间和电流强度加以控制。膜的厚度可控制在几微米到几毫米范围内。然而对于合金膜,由于各种金属离子沉积速率的差异,制备面积较大的膜时会出现组分分布不均的问题。
②无电镀法。控制自催化分解或降解亚稳态金属盐,在支撑体上形成薄膜。对钯膜,常使用的金属盐有Pa(NO3)4(NO2)2、 Pa(NH3)4Cl2,常用的降解(催化)剂为肼或次磷酸钠。通常,支撑体还需预处理以带有钯核,从而降低液相中的自催化反应。该法可在复杂表面形成厚度均匀、强度较高的膜,钯及其合金膜均可采用该方法制备。但控制膜的厚度尚有一定的困难,而且难于避免液相主体中的分解反应,导致不必要的损失;另外还难于确保膜的纯度,常含有1.5%左右的磷化物杂质。
③化学气相沉积法。控制温度等条件,气态的金属化合物在支撑体表面发生化学反应,经成核、生长而形成薄膜。
④铸造与压延法。该法既可以用来大规模制备金属薄板和薄膜,也可小规模使用,其过程包括高温熔融、铸炼、高温均质化、热压和冷压,再经多次重复冷压延和退火处理等步骤,直到预期的厚度。若熔融体的冷却速率足够快(105~109K/s),则可以得到金属玻璃的无定形材料。这种材料具有优良的性质,如高的机械强度、电导性质、催化活性、氢可逆储存能力、耐腐蚀性能等。制备过程中,随着金属箔厚度的减小,杂质污染问题突出,碳、硫、硅、氯、氧等可导致其机械强度显著下降,因此也对原料的纯度提出了更高的要求。冷压延时,通常会导致晶格的错位,理论和实践表明在错位的应力场中可积存过量的氢,因此,可提高钯及其合金溶解氢的能力,这种效应将在提高膜操作温度的退火过程中逐渐消失。目前使用高纯度金属钯已可制备厚度在1μm以下的膜。
⑤物理气相沉积法。固体金属在高真空(<1.3mPa)下蒸发、冷凝沉积在低温支撑体表面并形成薄膜。此法在制备金属及其合金膜中是一种非常实用的方法,物理气相沉积法可分为真空沉积、溅射沉积和粒子束沉积三种。金属在坩埚中被加热至(或高于)熔点,蒸气分压足以产生较高的沉积速率。钯在1550℃时很容易蒸发,并具有良好的沉积性能。Ilias等采用热蒸发法在多孔支撑体上制备出钯、银和铜膜,然而由于各组分的蒸气分压和蒸发速率差异,沉积金属合金尚有一定的困难。合金膜通常采用交替沉积或使用多个蒸发源的方法制备。溅射过程并不需要对金属进行加热,溅射靶上的金属原子被高速的氩等离子轰击出,并在支撑体上沉积。该法的优势在于原子间的蒸发速率相近,适于制备合金膜;蒸发速率较低,可制备超薄膜,另外低温也是其优点。使用物理气相沉积方法,膜层与支撑体的结合强度往往不高,因此必须对支撑体进行适当的预处理。采用上述方法也可在无机多孔膜上制备金属复合膜,这可大大提高金属膜的机械强度。Gryaznov等以及Mishchenko等采用溅射的方法制备出Pa-Ru合金膜。
(2)氧化物致密膜的制备 氧化物致密膜以对称结构为主,常采用挤出和等静压法成型,其制备过程包括粉料制备、成型和干燥烧结三个基本步骤。在致密化过程中膜伴随着明显的收缩,控制不当会导致膜出现裂纹缺陷,Itoh等用显微镜观察测定了烧结温度条件对膜高度和宽度的变化,随着烧结温度的提高,膜的高度和宽度均变小,表明膜趋于致密;但也不难发现高度与宽度的变化并不一致。这主要是由重力的影响所导致的。此外,烧结参数的确定还须考虑到材料的化学稳定性和结构稳定性。
(3)多孔膜的制备 工业用无机多孔分离膜主要由多孔载体,过渡层和活性分离层三层结构构成。①多孔载体的作用是保证膜的机械强度,对其要求是有较大的孔径和孔隙率,以增加渗透性,减少流体阻力。多孔载体的孔径一般在10~15μm左右,其形式有平板,管式以及多通道蜂窝状,后二者较为常见。多孔载体一般由三氧化二铝、二氧化锆、碳、金属、陶瓷以及碳化硅材料制成。②过渡层是介于多孔载体和活性分离层中间的结构,其作用是防止活性分离层制备过程中颗粒向多孔载体渗透。由于有过渡层的存在,多孔载体的孔径可以制备得较大,因而膜的阻力小,膜渗透通量大。根据需要,过渡层可以是一层,也可以是多层,其孔径逐渐减小,以与活性分离层匹配。一般而言,过渡层的孔径在0.2~5μm之间,每层厚度不大于40μm。③活性分离层是真正起分离作用的膜,它是通过各种方法负载于多孔载体或过渡层上,分离过程主要是在这层薄膜上发生的。分离膜层的厚度一般为0.5~10μm。现在正在向超薄膜发展,现已可以在实验室制备出几十纳米厚的超薄分离层。工业应用的分离膜孔径在4nm~5μm之间,并且正在向微孔膜领域发展。
无机膜按形状可分为管式(包括单通道和多通道)、平板式、多沟槽式、中空纤维式。商品化的多孔陶瓷膜的外形主要有平板、管式和多通道三种,一般多为支撑体、过渡层和分离层构成的多层非对称结构。
(1)多孔陶瓷支撑体的制备 支撑体的功能主要是为非对称膜如微滤膜、超滤膜和纳滤膜提供足够的机械强度,因此其厚度一般在1~2mm。支撑体的制备主要采用挤出法、流涎法、注浆法以及压制法成型,对于不同构型的膜采用不同的方法成型。表2-3列出成型方法和相应的构型。
表2-3 支撑体的成型方法与构型

①挤出成型法。在水或塑化剂中加入粉料和添加剂,经混合后,炼制成塑性泥料,然后利用各种成型机械进行挤出成型。该法为机械化作业方式,坯体的外形由挤出头的内部形状决定,坯体长度可根据需要截取,物料的性质和陈化过程、挤出机挤出头与花心的设计等是主要影响因素。
②流涎成型方法。用来制备厚度在几毫米的平板多孔陶瓷支撑体或对称膜,其过程包括浆料制备、流涎成型和干燥烧结三个步骤。粉料分散在液体中,加入分散剂、黏结剂和增塑剂,搅拌得到均匀的浆料,经过加料嘴不断地向转动的基带上流出,逐渐延展开来,干燥后得到一层薄膜。
(2)多孔膜的制备
①固态粒子烧结法。将无机粉料微小颗粒或粒度为0.1~10μm的超细颗粒与适当的介质混合分散形成稳定的悬浮液,成型后制成生坯,再经干燥,在1000~1600℃高温下进行烧结处理。此法一般用于制备微孔陶瓷膜或陶瓷膜载体,也可用于制备微孔膜。膜的质量受粉体的制备及分级、成型方法及干燥和烧结条件等因素影响。
②溶胶-凝胶法。该法以醇盐Al(OC3H7)3、 Al(OC4H9)3、 Ti(i-OC3H7)4、 Zr(i-OC3H7)4、 Si(OC2H5)4、 Si(OCH3)4或金属无机盐如AlCl3为原始原料,通过水解,形成稳定的溶胶。然后在多孔支撑体上浸涂溶胶,在毛细吸力的作用下或经干燥,溶胶层转变为凝胶膜,热处理后得到多孔无机膜。溶胶-凝胶法制无机膜的流程见图2-11。

图2-11 溶胶-凝胶法制无机膜的流程
该法制膜过程中的关键在于控制膜的完整性,即避免针孔和裂纹等缺陷的产生。研究表明,膜的完整性、膜的孔径都取决于溶胶、支撑体的性质以及凝胶膜的干燥和热处理条件。溶胶-凝胶技术可以制备出纳米级的超细粒子,商品化γ-Al2O3、TiO2和ZrO2超滤膜正是采用这一方法制备的。
③阳极氧化法。将高纯度金属箔(如铝箔)置于酸性电解质溶液(如H2SO4、H3PO4)中进行电解阳极氧化。氧化过程中,金属箔片的一侧形成多孔的氧化层,另一侧金属被酸溶解,再经适当的热处理即可得稳定的多孔结构氧化物膜。阳极氧化法制出的膜具有近似直孔的结构,控制好电解氧化过程,可以得到孔径均匀的对称和非对称两种结构的氧化铝膜。非对称氧化铝膜在气体、液体分离,尤其是生化产品的精制等方面有着一定的应用潜力。但是目前这一技术仅限于制备氧化铝膜,而且由于缺少支撑体,膜的强度较低,所以仅用于制备小面积平板膜,用于实验室研发及中试过程。
④分相法。利用硼硅酸玻璃的分相原理(图2-12),将位于Na2O-B2O3-SiO2 三元不混溶区内的硼硅酸玻璃在1500℃以下熔融,然后在500~800℃进行热处理,使之分为不混溶的Na2O-B2O3相和SiO2相,再用5%左右的盐酸、硫酸或硝酸浸提,得到连续又互相连通的网络状SiO2多孔玻璃。

图2-12 Na2O-B2O3-SiO2体系相图
分相法得到的膜孔径分布窄,比表面积可高达500m2/g,还可调节膜表面的Zeta电位以及与水的润湿性。因此,可用于气体分离和膜反应过程。另外高温下的玻璃熔融体容易成型,可以制备出纤维或管状膜。
⑤有机聚合物热分解。在惰性气体保护或真空条件下,将热固性聚合物高温热分解碳化。也可以将有机膜制成多孔无机膜,如用纤维素、酚醛树脂、聚丙烯腈(PAN)等有机物可以制备碳分子筛膜,用硅橡胶可以得到硅基质多孔无机膜。由于有机膜在热分解过程中的收缩率很大,如硅橡胶膜分解时收缩率在10%以上,从而导致膜出现缺陷,因此采用有机聚合物热分解法制备非对称膜较为困难。
⑥薄膜沉积法。是用溅射、离子镀、金属镀及气相沉积等方法,将膜材料沉积在载体上制造薄膜的方法。它分为膜材料 (膜料)的气化和膜材料的蒸气依附于其他材料(多孔陶瓷、玻璃或多孔不锈钢)载体上形成薄膜两个步骤。它是借鉴了传统的物理镀膜方法,是制备微孔金属膜或氧化物膜的技术。
⑦原位生长法。通常以聚合物膜及基底,在其上原位生长一层致密分离层,构成有机-无机杂化膜;原位生长法是制备金属有机骨架/聚合物杂化膜的常用方法之一。最为常用的方法为水热法(溶剂热法),是将前驱体与有机胺、去离子水、乙醇和甲醇等溶剂混合后放入密封容器,加热到一定的温度(25~250℃),在一定压力(1×103kPa)下反应,晶化成膜[27]。此外,水热法也可用于制备分子筛膜:a.将事先合成好的分子筛埋在相对非渗透性的基质中成膜;b.在多孔载体的孔口或次孔口原位水热合成分子筛膜。
⑧核径迹刻蚀法。用放射源产生的高能粒子(中子、α粒子)轰击绝缘的无机薄膜材料,如云母、玻璃等,然后再用腐蚀剂刻蚀被放射粒子轰击过的材料,即可得形状与孔径大小都均匀的直孔膜。
⑨聚合法。制备具有非碳骨架的无机聚合物膜,即具有氮磷骨架的合成无机聚合膜,它在100~350℃稳定,并且孔径可在一定范围内调节。
(3)无机多孔膜的修饰(改性) 采用浸渍或吸附的方法可将液相中改性组分沉积在膜的表面和膜孔内,也可用薄膜沉积技术(包括物理气相沉积、化学气相沉积和超临界流体沉积技术)对膜进行表面改性。膜经改性后,不仅可进一步减小其孔径(表2-4);还可改变膜孔表面的化学性质,从而改善膜的分离性能。
膜改性的目的包括:①减小孔径,满足微滤、超滤或气体分离的要求;或通过修饰将孔封闭,使微孔膜成为致密膜。②通过引入某些元素或化合物,调节微孔表面性质,从而达到改变膜的传递与分离机制。③引入某些具有催化性能的活性组分,使膜既具有分离性能又具有催化活性。
表2-4 膜改性结果

①α-TiO2:金红石氧化钛。