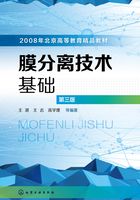
3.5 微滤膜的制备
制备微滤膜的材料分有机高分子和无机材料两大类。材料本身制约了所能选用的制膜方法、所能得到的膜形态及所能适用的分离原理。根据材料的种类,制备微滤膜的方法主要有相转化法、辐射固化法、溶出法、拉伸法、烧结法、核径迹法和阳极氧化法等。各种膜制备方法及其适用的材料范围见表3-4。
表3-4 各种膜制备方法及其适用的材料范围

根据膜材料和制备工艺的不同,微滤膜大体上可分为对称结构、不对称结构、核径迹蚀刻结构和复合结构(皮层和多孔亚层是两种材料)。微滤膜典型断面结构示意图见图3-8。图3-8 (a)为直通孔结构,制备方法为核径迹法;图3-8 (b)为曲通孔结构,制备方法为相转化法;图3-8 (c)为海绵状曲通孔结构,制备方法为相转化法;图3-8 (d)为细缝网络孔结构,制备方法为拉伸法;图3-8(e)为类指状孔结构,制备方法为相转化法;图3-8 (f)为单皮层结构,制备方法为相转化法;图3-8 (g)为双皮层结构,制备方法为相转化法;图3-8(h)为无机膜孔结构,制备方法为烧结法。其中图3-8(a)~(d)为对称微滤膜结构,图3-8(e)~(h)为不对称微滤膜结构。

图3-8 微滤膜典型断面结构示意图
3.5.1 相转化法[58,59]
相转化法是制取微滤膜最常用的方法,该技术应用时间较长,适应的膜材料比较广泛,技术相对比较成熟,使用的膜材料主要限制在高分子聚合物类,包括共混物、均聚物、天然或人工合成的嵌段共聚合物。根据溶剂、添加剂和凝固浴的不同,可分为溶剂蒸发凝胶法、浸渍凝胶法、热致相分离法等。
(1)溶剂蒸发凝胶法 首先将聚合物溶于某种溶剂,配成制膜液;然后将配好的制膜液浇铸并刮涂在适当的支撑物(平板玻璃、无纺聚酯、金属或聚合物如聚四氟乙烯)上,在一定的温度和气流速度下,在惰性环境中(如N2,不可含有溶剂的蒸气和水蒸气),随聚合物溶液内溶剂的蒸发,制膜液将发生相转化,即高分子制膜液开始由单相逐渐分离成两种极为均匀的分散相。无数极细的液滴散布到另一液相中,大部分高分子不断地聚集到小液滴的周围,而母液相中残留的高分子则越来越少。随着溶剂的继续蒸发,液滴相互接触。溶胶逐渐变成凝胶,最后形成一种分布均匀的致密膜(对称结构)(图3-9)。

图3-9 溶剂蒸发凝胶法制微滤膜示意图
【制膜示例1】 CA-CTA微滤膜的制备[60]
膜材料:CA、CTA;溶剂:二氯甲烷、丁醇;非 溶 剂:甘油、异丁醇。
制膜工艺:将18g二醋酸纤维素和10g三醋酸纤维素,在360mL二氯甲烷和40mL的丁醇混合溶液中溶解2h,然后再加入7mL的甘油和200mL的异丁醇,混合搅拌均匀,流延成平板膜,在20℃、湿度60%的条件下使溶剂蒸发干燥。
(2)浸渍凝胶法 先将聚合物溶于某种溶剂配成制膜液,将其刮涂在适当的支撑体(如无纺聚酯)上,最后浸入含有非溶剂(一般为水)的凝胶浴中,溶剂与非溶剂的扩散将导致凝胶。由传质和相分离两者共同决定膜的最终结构。由于铸膜液与凝胶液接触时表面最先转化为凝胶,故在膜表面形成致密的表层,在其下面则是疏松多孔结构。对于微滤膜而言,凝胶洗涤后就可直接使用。凝固浴介质一般为水,也可用有机溶剂,由于溶剂/非溶剂对的选择是影响膜结构的重要因素,所以不能随意选择非溶剂。影响制膜的因素还包括有聚合物的浓度、溶剂组成、添加剂组成、溶剂蒸发时间、环境温度和湿度、凝胶浴组成和凝胶浴温度等。
【制膜示例2】 加强型聚砜微孔滤膜的研制[61]
膜材料:PS(μ=0.51);溶剂: DMF;添加剂:环乙醇、庚烷、乙醚和邻苯二甲酸二丁酯(DBP);沉淀剂:DMF、水。
制膜工艺: 在PS-DMF溶液中,加入由环乙醇、庚烷、乙醚和DBP组成的混合添加剂,搅拌均匀,过滤,静置脱泡。用无纺布浸渍,通过间隙为0.1mm的刀架,在空气中溶剂蒸发60s以后,放入沉淀浴中洗去溶剂,在60℃下烘干,即得成品微滤膜。
(3)热致相分离法 热致相分离(TIPS)法则是利用一种潜在的溶剂来成膜,它在高温时为膜材料的良溶剂,低温时为膜材料的非溶剂,即热致相法具有“高温相溶、低温分相”的特点。使用TIPS法制备微孔膜有四步:①首先要选择一种高沸点、低分子量、在室温下是固态或液态的与给定聚合物不相容的稀释剂,当升高温度时,稀释剂能与聚合物形成均相溶液;②将溶液预制成所需要薄膜、块状或中空纤维等构形;③在冷却或等温淬冷过程中实现体系的液-液相分离;④一般可用溶剂萃取、减压等方法脱除分相后的凝胶中的稀释剂,再经干燥后即得到微孔材料。微孔材料的孔隙率、孔径大小、孔结构形态、聚合物稀释剂的性质、聚合物的浓度,特别是冷却速率等因素密切相关。工业上这四步可连续操作(图3-10)。

图3-10 TIPS法工业流程
TIPS法制备微孔滤膜具有下述优点:①可控制孔径及孔隙率大小;②可得到多样的孔结构形态(诸如蜂窝状结构、网状结构、树枝状孔等),并且孔径分布能做到相当窄;③膜材料的品种大大增加,很多结晶的、带有强氢键作用的共混高聚物在室温下难有合适的良溶剂,TIPS法大大扩充了对稀释剂的选择余地;④制备过程易连续化。当然,TIPS法的缺点和局限性为:①TIPS膜本身难薄化,易折断,易形成表面皮层;②膜内的孔易呈封闭或半封闭式,对膜污染的抵抗性较低;③当采用较高的冷却速率进行生产时,对生产设备的要求比较高,生产能量耗损大,增加了成本,影响了经济可行性。
聚丙烯由于其优越的物理化学性能、生物化学性能及丰富的来源、低廉的成本、良好的疏水性,而受到研究者的关注。
【制膜示例3】 聚丙烯微滤平板膜的制备[62]
膜材料:等规聚丙烯(iPP)(非极性的结晶高聚物);稀释剂:邻苯二甲酸二丁酯(DBP)。
制膜工艺:取一定量扬子石化产F401 iPP(熔体指数MI为2.5g/10min),加入适量的稀释剂DBP;原料混置于一锥形瓶内,瓶内充满了氮气(防止iPP氧化降解),密封; 在250~270℃酸浴内加热20~26min,
期间不断搅拌并连续充入氮气。体系制成均相溶液,静置脱泡至无气泡产生,将瓶快速从酸浴中移出,并将料液流涎到一定温度的不锈钢板上(不低于75℃),然后迅速放入确定温度的水浴中淬火;取出样品,浸入萃取剂中萃取5~6h;取出样品放入干燥箱中,40℃恒温烘30min后即可得成品。
表3-5是不同组分在10℃±2℃水浴制成的膜的性能,图3-11是热致相分离法制得的iPP微滤膜的SEM图像。

图3-11 iPP热致相分离法制得的微滤膜的SEM图像
表3-5 不同组分在10℃±2℃水浴制成的膜的性能

(4)其他方法[63] 除了以上3种主要的相转化法以外,还有2种由于技术落后而不常用的方法。
①蒸气相沉淀。早在1918年Zsigmondy就曾使用此法。将由聚合物和溶剂组成的刮涂薄膜置于被溶剂饱和的非溶剂蒸气气氛中。由于蒸气相中溶剂浓度很高,防止了溶剂从膜中挥发出来,随着非溶剂扩散到刮涂的薄膜中,膜便逐渐形成。使用这种方法可以得到无皮层的多孔膜。
②控制蒸发沉淀。早在20世纪初就曾被采用。它是将聚合物溶解在一个溶剂和非溶剂的混合物中(这种混合物作为聚合物的溶剂),由于溶剂比非溶剂更容易挥发,所以蒸发过程中非溶剂和聚合物的含量会越来越高,最终导致聚合物沉淀并形成带皮层的膜。
3.5.2 溶出法
溶出法是在制膜基材中混入某些可互溶的水溶性高分子材料或其他可溶的溶剂或与水溶性固体细粉混炼,成膜后用水或其他溶剂将水溶性物质溶出,从而形成多孔膜。例如常将食盐、碳酸钙等细粉混入聚合物中制膜,最后以水或酸将其溶出即得多孔膜。
【制膜示例4】 溶出法制备二醋酸纤维素微滤膜[64]
膜材料:二醋酸纤维素;增塑剂:聚乙二醇;溶剂:丙酮、二氯甲烷。
制膜工艺:将CA和PEG共溶于混合溶剂中,将配成的沉液在玻璃板上刮膜后,让沉剂蒸发,再用水将致孔的聚乙二醇溶出后,剩下空隙部分。
3.5.3 浸出法(分相法)[65]
浸出法是选择合适的溶剂将薄膜中的一种组分浸取出去,从而形成多孔膜,用于无机膜材料的玻璃微孔膜的制备。利用的是硼硅酸玻璃的分相原理(图3-12),将位于Na2O-B2O3-SiO2三元不混溶区内的硼硅酸玻璃在1500℃以上熔融,然后在500~800℃进行热处理,使之分为不混溶的Na2O-B2O3相和SiO2相,再用5%左右的盐酸、硫酸或硝酸浸提,得到连续又互相贯通的网络状SiO2多孔玻璃膜[66],常见的Vycor玻璃膜就是利用这一方法制备的,其孔径分布见图3-13,平均孔直径在4nm左右。

图3-12 三元体系相图

图3-13 玻璃膜孔径分布图
McMilan和Maddison[67]用TiCl4浸渍多孔膜,热处理得到TiO2改性多孔玻璃膜。Eguchi等用相似方法制备出ZrO2改性管状玻璃膜,膜孔径在0.020~2μm之间(图3-14)[68]。浸出法可以通过控制配料组成、分相温度和酸抽提条件制备出孔径在20~2000nm的多孔玻璃膜。原料液中Na2O/B2O3比例越大,分相温度越高,膜孔径越大;提高分相温度并延长分相时间,可使膜的孔径分布变宽。该法制得的膜孔径分布窄,比表面积高达500m2/g,还可调节膜表面的zeta电位以及水的润湿性,常用于气体分离和膜反应过程。另外高温下的玻璃熔融体容易成型,可制备出纤维或管状膜。但受制备技术的限制,膜的薄化和复合比较困难。因此,对称结构的多孔玻璃膜因渗透阻力较大,在应用方面受到了很大限制。

图3-14 玻璃膜的表面改性
3.5.4 核径迹蚀刻法
核径迹蚀刻法是由放射性同位素裂变而产生高能粒子辐射(辐射强度一般为1MeV),垂直撞击膜材料薄片,使材料本体受到损害而形成径迹,然后用浸蚀剂腐蚀掉径迹处的本体材料,将此径迹扩大,形成具有很窄孔径分布的圆柱形孔,即成一种直通孔的微滤膜(图3-15)。这种膜对微粒的吸附或阻留较普通微孔膜孔径小得多。因此,对于胶体、金属等贵重物质的处理有一定价值;其结构为几何直孔。其孔径范围为0.02~10μm。核孔膜断面结构示意图见图3-16,其开孔率约15%,孔密度为(2~3)×107个/cm2。该膜具有亲水、低通量等特点,同时孔隙率也低(最大约10%)(图3-16)。核孔膜与普通纤维素膜横断面的比较见图3-17。

图3-15 高能粒子穿过聚合物的过程示意图[69]

图3-16 核孔膜断面结构示意图[70]

图3-17 核孔膜与普通纤维素膜横断面的比较
【制膜示例5】 聚碳酸酯核孔膜的制备
膜材料:聚碳酸酯(PC)薄膜[71];腐蚀剂:氢氧化钠。
制膜工艺:重离子轰击PC薄膜,使薄膜里聚合物分子键断裂,形成小分子和自由原子团,这些受激产物在紫外线/过氧化剂的作用下,继续损伤并形成酸性化合物,酸性化合物在碱溶液作用下,生成可溶性盐。经冲洗,形成微孔。PC核孔膜的典型制备流程图如图3-18所示,PC核孔膜的表面放大SEM照片如图3-19所示。

图3-18 PC核孔膜的典型制备流程图

图3-19 PC核孔膜的表面放大SEM照片
3.5.5 拉伸法
Calanese公司在20世纪70年代中期发展了一种新型的微孔膜制备方法,并推出了Celgard聚丙烯微滤商品膜。采用拉伸致孔,即先做成硬弹性膜,在单轴拉伸致孔后定形得到微滤膜。单轴拉伸的平膜横向力学性能极差,横向的拉伸强度仅为10MPa,易撕裂。
拉伸的基本方法是在相对低的熔融温度和高应力下挤出膜或纤维。聚丙烯分子则沿拉伸方向排列成微区、成核,形成垂直于拉伸方向的链折叠微晶片;之后在略低于熔点温度下热处理,链段可运动使结晶增长变硬,在结晶的表面上高分子链折叠而不融化在一起,最终形成所需的膜。只有半结晶的材料(如聚四氟乙烯、聚丙烯、聚乙烯等)才能用这种方法制膜。
商品化的Celgard聚丙烯拉伸微孔膜的孔呈细长形,长约0.1~0.5μm,宽约0.01~0.05μm。其孔结构为非真实性结构。制得膜的孔径范围为0.1~3μm,孔隙率可高达90%。商品化的膜还有聚四氟乙烯Goretex膜,可供特种行业使用,可过滤腐蚀性液体。拉伸法不需任何添加剂,无污染,适合于大规模工业化生产。拉伸法生产成本相对相转化法要低得多。PTFE拉伸膜的SEM照片和PP拉伸膜的SEM照片见图3-20、图3-21。

图3-20 PTFE拉伸膜的SEM照片[72]

图3-21 PP拉伸膜的SEM照片[73]
【制膜示例6】 拉伸法制备PET纤维[74]
膜材料:PET;溶剂:三氟乙酸、二氯甲烷。
制膜工艺:①纺丝。将干燥后的超高分子量PET样品,在室温下,用三氟乙酸/二氯甲烷的混合溶剂(体积比为7∶3)溶解3天左右,将纺丝原液倒入已经配好的纺丝管中,以水为凝固剂,在室温下进行干湿法纺丝,喷丝头为单孔,孔径为0.2mm。②拉伸。首先对初生纤维在室温下进行冷拉伸,一道拉伸温度低,拉伸丝的取向度较高,结晶较低,这种结构对后续的二道拉伸有利。然后在230℃的温度下进行二道热拉伸。由于在一道拉伸过程中产生了结晶,因此要求二道拉伸的温度要高于PET的结晶熔融温度,用以熔融原有晶区,实现纤维结构的重排。③热处理。以乙二醇为热处理介质,处理时间为3min。适当的热处理,可以改善纤维的结构,提高纤维热学性能。热处理时间对其力学性能影响最大,随时间的延长,膜性能下降。
3.5.6 辐射固化
E.shchodri等利用丙烯酸基团的特性进行辐射固化微备微孔膜[75]。有各种丙烯酸单体和丙烯酸功能化树脂。由于丙烯酸基团数和骨架的化学结构不同,所产生的高聚物的机械化学性能也大不相同。
辐射固化技术基于丙烯酸冠状树脂和单体在惰性非挥发性溶剂中发生聚合反应。聚合和相转化反应在极短的时间内同时发生。将溶液进行涂层,在中压水银灯或电子束下以10~100m/min的速度进行固化。由辐射隔室产生的涂层是一种无光泽膜,充满初始成孔的溶剂。在干清洁过程中,用具有惰性、安全、低蒸发热的特点的Freon溶剂萃取去除非挥发性溶剂。清洗机是一闭路装置。蒸气和溶剂在装置内连续不断地蒸馏,并返回进入系统,损失极少,所制备的微孔膜,白色而无光泽,具有均匀的孔隙率,孔径范围为0.05 ~0.5μm。膜的电子扫描图见图3-22。用紫外线或电子束高速交联单体和低聚物时,孔径结构清晰。当用紫外线固化时,涂层液中需要添加光诱发剂;而当用电子束固化时直接断裂各种化学键,不需要添加诱发剂。Freon是目前已知唯一适合于清洗的萃取剂。PTFE粉末烧结制出膜的SEM图见图3-23。

图3-22 辐射固化膜表面的SEM图(70000倍)

图3-23 PTFE粉末烧结制出膜的SEM图
辐射固化的固化速度和清洁方法使其在成本上优于其他技术。更重要的特点是通过使用多种多样的丙烯酸树脂和功能化单体作为固化的材料,便可获得具有多种化学性能的微孔膜。由于膜的表面具有侧全氟基,除二乙醚和氟化溶剂外,这种膜排斥所有有机溶剂,可应用在一些特殊的化工传递过程中。
3.5.7 烧结法
烧结法是一种简单的制备多孔膜的方法,特别是制备大孔基体,可以制有机膜也可以制无机膜。具体方法是将一定大小颗粒的粉末进行压缩,然后在高温下烧结。制得的孔径大约为0.1~10μm,孔隙率较低(10%~20%),异常耐热,结构为不对称管式,面积/体积比低,常为微滤膜,例如Carbosep(碳涂氧化锆)。聚合物粉末(聚乙烯、聚四氟乙烯、聚丙烯)、金属材料(不锈钢、钨)、陶瓷(氧化铝、氧化锆)、石墨(碳)和玻璃(氧化硅)等可采用此法制膜。ZrO2粉末烧结膜SEM图见图3-24。

图3-24 ZrO2粉末烧结膜SEM图
【制膜示例7】 原位造粒法制备γ-Al2O3微孔陶瓷膜[76]
制膜工艺:按预定的聚合铝Al13(OH)26Cl13(H2O)24,把铝箔放入稀盐酸中,回流加热,直到铝箔全部溶解,所得到的溶液趁热抽滤,冷却后备用。将市售的陶瓷板切割成圆板作为基片,选它的一个圆面作为浸渍面,浸渍时间为4s,浸渍后轻轻振荡,使浸渍液均匀地分布于整个浸渍面。把浸渍后的陶瓷片放入干燥器内(干燥器内已放入一瓶浓氨水),氨熏48h。把处理后的陶瓷膜以1℃/min的升温速度焙烧,当温度升到600℃时恒温3h。然后自然冷却到室温,就得到了一次浸渍膜。将上述干燥-烧结过程重复一次就得到了二次浸渍膜。二次浸渍膜比一次浸渍膜性能稳定,缺陷少,完整性更好。
【制膜示例8】 粒子烧结法制备氧化锆制滤膜[77]
制膜工艺:
(1)选择适当的支撑体 由于氧化锆的熔点高于氧化铝,制备氧化锆支撑体需要很高的烧结温度,而且氧化锆材料的成本远高于氧化铝。目前尚无商品氧化锆支撑体,因此选用α-Al2O3作为支撑体。支撑体的平均孔径为0.8μm。
(2)制备悬浮液 采用处理后的商品氧化锆微粉,平均粒径0.44μm左右。通过实验筛选,选取加入一定添加剂的沉液悬浮氧化锆微粉,并控制pH值在合适的范围,制得稳定的制膜液。
(3)涂膜 实验采用旋转涂膜法和浸浆法,控制一定的涂膜条件,使得成膜厚度在20μm左右。
(4)烧结 在不同温度和时间下烧结成膜。详细情况可见文献。
膜性能:较佳情况下制成的膜的平均孔径如图3-25所示。

图3-25 膜的孔径分布图
3.5.8 阳极氧化法[78]
20世纪20年代研究者为提高铝制品表面耐磨、耐腐蚀以及着色等性能,开展了阳极氧化的方法,在金属铝表面生成一层多孔氧化铝功能薄膜。1959年Hoar和Mott 将此方法用于氧化铝膜的制备,并深入研究了铝的阳极氧化过程与膜结构的关系。
阳极氧化法是将高纯度金属箔(如铝箔)置于酸性电解质溶液(如硫酸或磷酸)中进行电解阳极氧化。在氧化过程中,金属箔的一侧形成多孔的氧化层,另一侧金属被酸溶解,再经适当的热处理,即可得到稳定的多孔氧化铝膜。
阳极氧化法制出的膜具有近似直孔的结构,控制好电解氧化过程,可得到孔径均一的对称和非对称膜。1986年英国的Anotec Separation 公司采用阳极氧化法制出孔径200nm的对称膜和非对称膜,其孔隙率高达65%以上。但是,目前这一技术仅能在实验室范围内用于制备氧化铝膜,而且机械强度较低。
总之,各种制膜方法都有其局限性。相转化法局限于在常温下能溶于溶剂的高分子材料。热致相转化法(拉伸法)则可将制备不对称膜的对象扩展到常温下不溶的结晶性高分子材料。利用光聚合分相的Sumbeam Process 是生产率极高的制备微滤膜的工艺。目前的研究方向为核迹径法、辐射聚合、拉伸法等污染少的制膜工艺。