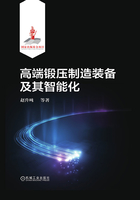
4.2 多连杆压力机的主要结构
现有的多连杆机构按照连杆数量划分,主要包括三大类,分别是六连杆机构、八连杆机构和十连杆机构。
4.2.1 六杆机构多连杆压力机
六连杆结构的压力机可用于较厚钢板的冲孔、落料、成形等冲压工艺,一般用于大工艺力的冲压工作,如在一次冲压工作中完成重型货车大梁的落料、成形、冲孔等。其主要特点是机身机构紧凑、刚性强,冲压和工艺力比同类型的曲柄连杆机构的机械压力机大,满负荷的工作区域较长,下死点附近速度小,工作效率高。曲柄肘杆机构如图4-1所示,六连杆传动机构如图4-2所示。

图4-1 曲柄肘杆机构
1—曲柄 2—连杆 3、4—肘杆 5—滑块

图4-2 六连杆传动机构
1—调速杆 2—摆杆 3—偏心轴 4—连杆 5—导轨 6—滑块
由于六连杆传动机构设计变量较多,运动复杂,目前采用优化设计方法,多是通过建立优化数学模型,编制优化计算程序,实现最优传动机构方案设计。但是在板料拉延成形过程中,为提高拉延件成形质量,一方面要求压力机在负载工作阶段具有均匀的冲压速度,另一方面却又要求滑块接触板料时速度较低。而上述研究都没有将滑块接触板料速度作为优化目标;同时,上述研究均未考虑由传动机构结构设计带来的运动干涉问题,这也就导致相应的优化结果难以应用到实际工程中。
4.2.2 八杆机构多连杆压力机
目前国内外机床行业主要应用的八杆机构如图4-3和图4-4所示。整个传动结构由偏心轴、摇架、上连杆、下连杆、角架及导柱组成。这种结构的压力机适用于薄板冲压成形、深拉深等工艺工作,多用于大型薄板覆盖件的大批量生产。八连杆结构的压力机,其模具在深拉深工作区域的冲击力很小,满负荷的工作区域长,但由于传动系统结构复杂,要求加工调试的精度高,使得制造周期长,因此成本高。

图4-3 八杆机构的三维模型

图4-4 对称八杆结构
除此种八杆机构外,还有一种对称八杆机构和一种双肘杆机构在压力机上也时有应用,其结构形式如图4-5和图4-6所示。

图4-5 另一种对称八杆结构

图4-6 双肘杆机构结构示意图
对图4-4所示结构的分析表明,在给定杆系结构参数的情况下,滑块的冲压行程占整个工作周期较短,其他行程时间较长,因此冲压工作利用效率低,冲压行程滑块的位置变化大,未能起到很好的保压作用,但是滑块的加速度相对较小,避免工件承受突变力作用,有利于提高冲压产品的质量。
对于此种结构而言,可以将其改进方向重点放在杆系结构参数的调整优化上,提升其在保压时间、滑块工作行程位置保持等方面的性能。
八杆机构的杆系原理如图4-7所示。

图4-7 八杆式压力机杆系原理
总体而言,八杆机构的特点主要表现在以下几个方面:①工作行程较长且在行程中基本都是满载荷,因此特别适合比较细长零件的加工;②滑块带动的模具工作时所受到的冲击力比较小且平缓;③它的传动系统结构比较复杂,在对杆件进行加工和装配时的精度要求很高;④它的设计制造周期一般都很长,这就造成了加工制造成本较高。
4.2.3 十杆机构多连杆压力机
十杆机构主要应用于双动压力机外滑块主驱动,其原理如图4-8所示。

图4-8 十杆机构结构简图
十杆机构常用于闭式双动机械压力机外滑块主传动驱动上。其主要特点是能保证滑块在拉深区域工作时,外滑块能够按要求压边并保证压边力在内滑块的整个拉深过程中不变化,达到拉深件不拉裂、不起皱的要求,从而保证拉深件的质量。
但相对于前面的六杆机构与八杆机构而言,十杆机构的适用范围并没有得到最大范围的扩展。之所以造成此种情形,一是因为现有的六杆机构和八杆机构已经能够满足大多数的加工工艺要求,因此对于新的结构并没有太过旺盛的需求。二是因为虽然多连杆式压力机出现的时间已经不短,但前期的研究主要在六杆机构与八杆机构的开发应用上,行业内并未对十杆机构的研究投入太多的精力。但是随着社会的发展,加工行业对于高精度、高质量、高稳定性、高可控性的机床的需求会越来越旺盛,现有的装备技术也将越来越难以满足其工艺要求,这就要求对于除六杆机构和八杆机构之外的其他结构进行更加深入的研究。
从上面的分析可以看出,相对于一般的曲柄连杆式压力机而言,多连杆机械式压力机拉延时速度低且均匀,而空行程速度快,生产率高。多连杆压机拉深深度大,在允许的速度内,多连杆压机拉延深度可达320mm,而一般曲柄压机只有70mm左右。多连杆压机能以较小的偏心距实现大的滑块行程长度,更好地满足拉深工艺需要和自动化上下料的需要;而且在工作过程中多连杆机械压力机能有效减小对模具的冲击,提高了模具的使用寿命。
多连杆机械式压力机的滑块在工作过程中速度较低且近似为匀速运动,低速运动能有效地降低材料的变形,符合板料冲压过程对速度的要求,可以有效提高成形件的质量。与此同时,由于减少了系统的动态载荷,从而提高了模具的使用寿命,降低了整个机械系统的振动和冲击产生的噪声,优化了工作环境。此外,滑块空行程时运动速度较高,具有急回的特性,滑块运行的循环时间大大缩短,压力机的行程次数大大提高。
而将六杆机构、八杆机构和十杆机构综合比较的话就会发现,六杆机构压力机在下死点附近的速度较小;八杆机构在其负荷工作区域内的速度几乎为恒速;十杆机构驱动的双动压力机外滑块在其下死点时,行程在较长时间内处于几乎停止的状态,以保证内滑块完成整个拉深工作行程。
4.2.4 其他结构多连杆压力机
除常用的六杆机构、八杆机构及十杆机构外,国内外目前还在进行其他传动结构的研究,如可控六杆机构、混合驱动七杆机构、混合驱动九杆机构等。
1.可控六杆机构
可控六杆机构的传动如图4-9所示,从图中可以看出此机构为二自由度机构,这一点与类四杆五杆机构相似,因此当机构的两输入运动都由常规电动机提供时,将此机构称为类五杆六杆机构。类五杆六杆机构通过改变或修正五杆机构的结构形式,使机构在常规电动机的驱动下减小运动补偿量,所输出的轨迹更接近要实现的轨迹,从而降低对伺服电动机的要求,既能很好地实现给定运动又具有较好的动力学性能。此机构在原五杆机构的基础上引入了调节杆2,在机构的机械部分加入了可调环节(由杆1、杆2以及齿轮构成),这样构造的混合驱动可控机构系统有机械可调部分和可控电动机(杆5)两个柔性环节,其机构特性仍然具有混合驱动可控机构的优点,且系统结构相对简单、柔性大大增加。

图4-9 可控六杆机构结构简图
此类五杆六杆机构不但具备了原混合驱动五杆机构和类四杆五杆机构的优点,而且与上述两机构相比,此机构的运动输出轨迹更为丰富,输出运动特性更易于调整,能够很好地实现上述想法。在实现给定轨迹时可大大减小伺服电动机的运动补偿量,使机构获得良好的动力学性能成为可能。
2.混合驱动的七杆机构
混合驱动七杆机构的传动结构如图4-10所示。多杆压力机结构复杂,它要求的制造精度和装配精度很高,最关键的是一旦它的结构确定下来,滑块的输出加工曲线也就定了下来,只能在一定程度上改善压力机的性能,完全没有柔性。因此,它并不能满足现代制造中柔性制造的要求。混合驱动七杆结构压力机就是为了解决多连杆压力机的此种问题而研制的。

图4-10 混合驱动的七杆机构示意图
用于混合驱动的七杆机构必须要有三个活动构件通过运动副连接到机架上,其中两个作为输入,一个作为输出。而且每一个节点轴的运动要求不完全依赖于其他某一个轴的运动,而是依赖于另外两个轴的组合运动。
现有设计过程是从分析混合驱动七杆机构的奇异性入手,对混合驱动七杆机构的可动性条件进行了分析,讨论了避免奇异位形的条件,给出了可动性条件。然后,从正运动和逆运动学两方面对该混合驱动可控压力机进行运动学分析。计算出了七杆机构各个构件的位置、速度、加速度。正运动学分析就是已知常速电动机和伺服电动机的运动学参数求滑块的运动学参数。逆运动学就是已知常速电动机和滑块的运动学参数求伺服电动机的运动学参数,从而达到控制伺服电动机的目的。从实际的应用来看,逆运动学分析的意义更大。
3.六杆机构伺服压力机
现有的六杆机构主要包含三类,一类是基本的曲轴-肘杆机构。此种结构的压力机主要根据上下两个连杆的长度是否相等分为等长肘杆机构与不等长肘杆机构。两种机构的滑块行程和工作行程都不大,增力效果根据两连杆的长度可以进行调节。
还有一类是三角肘杆机构,其结构如图4-11~图4-13所示。其中图4-11所示为上三角肘杆机构,图4-12所示为中央三角肘杆机构,图4-13所示为下三角肘杆机构。这三种结构中,上三角肘杆机构相对于普通肘杆机构而言,最大速度偏高,但是平均速度略低于普通肘杆机构,加工效率偏低。同时最大加速度明显大于普通肘杆结构。而过大的加速度会增加机构的惯性力,从而增加电动机的负载。工作行程内上三角肘杆机构同普通肘杆机构所能提供的压力相比相差不大。所以上三角肘杆机构的主要优化方向为减小机构的加速度的同时提升其在增力比方面的优势。

图4-11 上三角肘杆机构

图4-12 中央三角肘杆机构

图4-13 下三角肘杆机构
图4-12所示的中间三角肘杆式传动机构和肘杆机构的速度及加速度和位移的关系曲线基本相似。二者速度-位移曲线几乎重合。前者的滑块加速度在上死点附近有剧烈的变化,后者则比较平稳。但中央三角肘杆机构在距下死点150mm的距离内的增力比都保持在4以上,这是普通的肘杆机构所不能比拟的。相对于上三角肘杆机构与中央三角肘杆机构而言,下三角肘杆机构的性能同普通的曲轴-肘杆相比并没有什么特别突出的地方。
除了上述提到的两大类六杆机构外,还有包括对称六杆机构等其他机构,其传动结构如图4-14所示。

图4-14 对称六杆机构